Destylator przemysłowy to urządzenie wykorzystywane w procesach separacji cieczy na podstawie różnicy w temperaturze wrzenia. Jego głównym celem jest oddzielenie składników mieszaniny, co ma kluczowe znaczenie w wielu branżach, takich jak chemiczna, farmaceutyczna czy petrochemiczna. Proces destylacji polega na podgrzewaniu cieczy do momentu, gdy zaczyna ona parować, a następnie schładzaniu pary, aby przekształcić ją z powrotem w ciecz. W praktyce oznacza to, że destylator składa się z kilku kluczowych elementów, takich jak zbiornik do podgrzewania, kolumna destylacyjna oraz kondensator. W zależności od zastosowania, destylatory mogą mieć różne konstrukcje i rozmiary, od małych urządzeń laboratoryjnych po ogromne instalacje przemysłowe. Ich wydajność oraz efektywność są często kluczowymi czynnikami wpływającymi na rentowność produkcji.
Jakie są rodzaje destylatorów przemysłowych i ich zastosowanie
W przemyśle istnieje wiele rodzajów destylatorów, które różnią się konstrukcją oraz zastosowaniem. Najpopularniejsze z nich to destylatory prostokątne, kolumnowe oraz frakcyjne. Destylatory prostokątne są najprostsze w budowie i najczęściej stosowane w małych zakładach produkcyjnych. Działają na zasadzie jednofazowej destylacji i są idealne do separacji składników o znacznej różnicy temperatur wrzenia. Z kolei destylatory kolumnowe charakteryzują się większą efektywnością i są wykorzystywane w dużych zakładach przemysłowych do separacji wielu składników jednocześnie. Dzięki zastosowaniu kolumny z wypełnieniem możliwe jest uzyskanie wyższej czystości produktów końcowych. Destylatory frakcyjne natomiast pozwalają na bardziej skomplikowane procesy separacji, gdzie różnice temperatur wrzenia są niewielkie. Stosuje się je głównie w przemyśle petrochemicznym do uzyskiwania różnych frakcji ropy naftowej.
Jakie są kluczowe zalety stosowania destylatorów przemysłowych
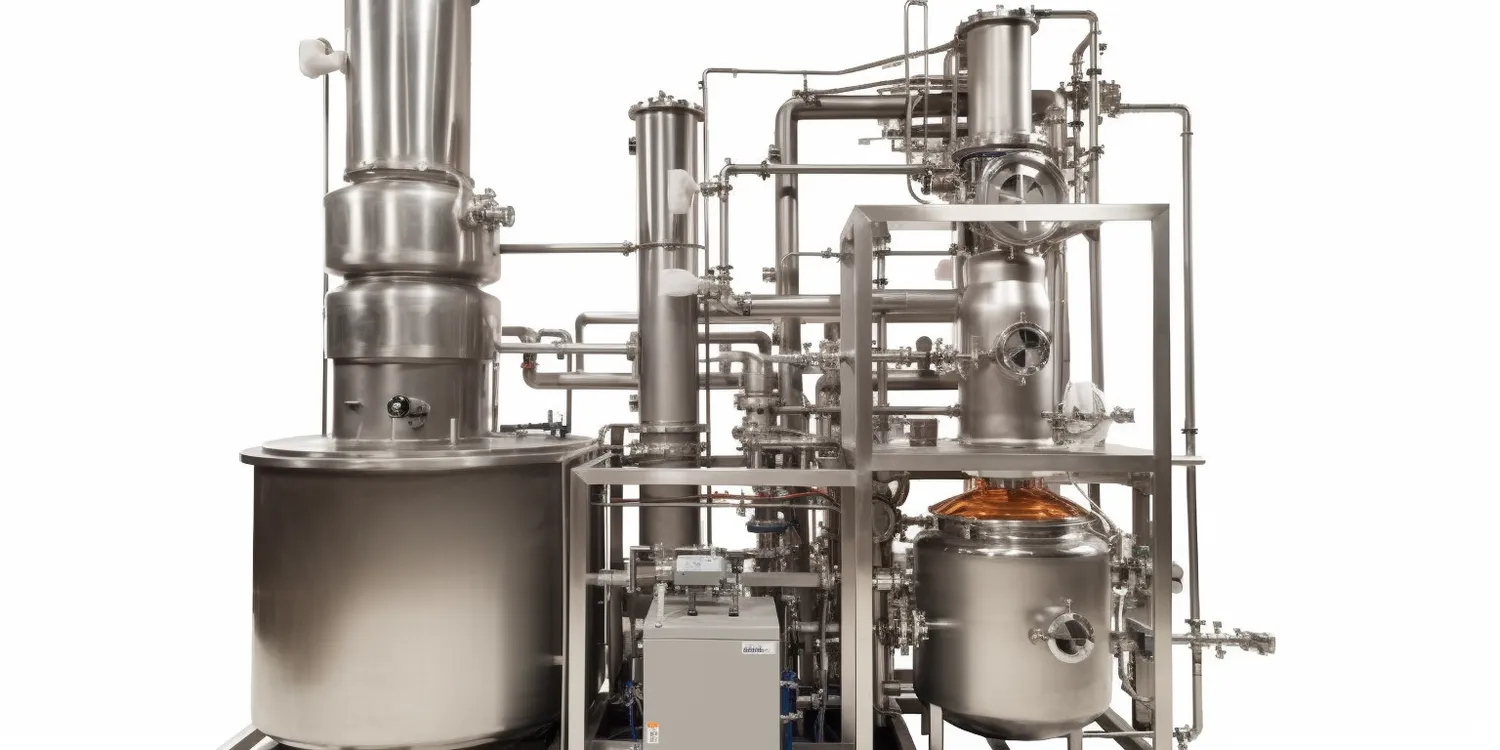
Stosowanie destylatorów przemysłowych przynosi wiele korzyści zarówno dla producentów, jak i dla końcowych użytkowników produktów. Przede wszystkim umożliwiają one efektywne oddzielanie składników chemicznych, co jest niezbędne w wielu procesach produkcyjnych. Dzięki temu można uzyskać wysokiej jakości substancje chemiczne o określonych właściwościach fizykochemicznych. Kolejną istotną zaletą jest możliwość automatyzacji procesu destylacji, co znacznie zwiększa wydajność produkcji oraz redukuje ryzyko błędów ludzkich. Nowoczesne systemy sterowania pozwalają na precyzyjne monitorowanie parametrów pracy destylatora, co przekłada się na lepszą kontrolę jakości produktów końcowych. Ponadto, stosowanie destylatorów przyczynia się do oszczędności energii poprzez optymalizację procesów grzewczych i chłodniczych. Warto również wspomnieć o ich wszechstronności – mogą być wykorzystywane w różnych branżach, od produkcji alkoholu po rafinację ropy naftowej.
Jakie czynniki wpływają na wybór odpowiedniego destylatora przemysłowego
Wybór odpowiedniego destylatora przemysłowego jest kluczowym krokiem dla każdej firmy zajmującej się produkcją chemiczną czy pokrewnymi branżami. Istnieje wiele czynników, które należy wziąć pod uwagę przy podejmowaniu decyzji o zakupie tego typu urządzenia. Po pierwsze, należy dokładnie określić wymagania dotyczące procesu technologicznego oraz rodzaj substancji, które mają być poddawane destylacji. Różne substancje mają różne właściwości fizykochemiczne, co może wpłynąć na wybór konkretnego typu destylatora – prostokątnego, kolumnowego czy frakcyjnego. Kolejnym istotnym czynnikiem jest wydajność urządzenia oraz jego zdolność do pracy w określonych warunkach ciśnienia i temperatury. Ważne jest również uwzględnienie kosztów eksploatacji oraz konserwacji urządzenia – im bardziej skomplikowana konstrukcja, tym wyższe mogą być koszty związane z jej utrzymaniem. Należy także zwrócić uwagę na dostępność części zamiennych oraz serwis posprzedażowy oferowany przez producenta.
Jakie są najnowsze technologie w destylacji przemysłowej
W ostatnich latach technologia destylacji przemysłowej przeszła znaczną ewolucję, co pozwoliło na zwiększenie efektywności procesów oraz poprawę jakości uzyskiwanych produktów. Jednym z najważniejszych trendów jest automatyzacja procesów, która umożliwia zdalne monitorowanie i kontrolowanie pracy destylatorów. Dzięki zastosowaniu zaawansowanych systemów informatycznych i czujników, operatorzy mogą na bieżąco śledzić parametry pracy urządzenia, takie jak temperatura, ciśnienie czy przepływ. To z kolei pozwala na szybką reakcję w przypadku wystąpienia nieprawidłowości, co minimalizuje ryzyko awarii i przestojów produkcyjnych. Innym istotnym kierunkiem rozwoju są technologie związane z odzyskiem energii. Nowoczesne destylatory często wyposażone są w systemy umożliwiające recykling ciepła, co znacznie obniża koszty eksploatacji i wpływa na ochronę środowiska. Zastosowanie materiałów o wysokiej przewodności cieplnej oraz innowacyjnych rozwiązań konstrukcyjnych pozwala na jeszcze lepsze wykorzystanie energii podczas procesu destylacji.
Jakie są wyzwania związane z użytkowaniem destylatorów przemysłowych
Pomimo licznych zalet stosowania destylatorów przemysłowych, istnieje również szereg wyzwań, które mogą wpłynąć na ich efektywność oraz bezpieczeństwo użytkowania. Jednym z głównych problemów jest konieczność regularnej konserwacji i czyszczenia urządzeń, aby zapewnić ich prawidłowe działanie. Zanieczyszczenia mogą prowadzić do obniżenia wydajności procesu oraz wpływać na jakość uzyskiwanych produktów. Dlatego ważne jest, aby firmy wdrożyły odpowiednie procedury utrzymania ruchu oraz planowały regularne przeglądy techniczne. Kolejnym wyzwaniem jest zarządzanie odpadami powstającymi podczas procesu destylacji. Wiele substancji chemicznych może być szkodliwych dla środowiska, dlatego konieczne jest wdrożenie odpowiednich systemów zarządzania odpadami oraz ich utylizacji zgodnie z obowiązującymi normami prawnymi. Dodatkowo, zmieniające się regulacje dotyczące ochrony środowiska oraz bezpieczeństwa pracy mogą wymuszać na firmach dostosowanie swoich procesów produkcyjnych do nowych wymogów.
Jakie są koszty związane z zakupem i eksploatacją destylatora przemysłowego
Koszty zakupu i eksploatacji destylatora przemysłowego mogą się znacznie różnić w zależności od jego typu, wielkości oraz zastosowania. Na początku należy uwzględnić koszty zakupu samego urządzenia, które mogą być znaczące, zwłaszcza w przypadku dużych instalacji kolumnowych czy frakcyjnych. Warto jednak pamiętać, że inwestycja w wysokiej jakości destylator może przynieść długofalowe korzyści finansowe poprzez zwiększenie wydajności produkcji oraz poprawę jakości produktów końcowych. Poza kosztami zakupu należy także brać pod uwagę wydatki związane z instalacją oraz uruchomieniem urządzenia. Koszty te mogą obejmować zarówno prace budowlane, jak i montażowe oraz kalibrację systemu sterowania. Eksploatacja destylatora wiąże się również z bieżącymi kosztami operacyjnymi, takimi jak zużycie energii elektrycznej czy paliwa do podgrzewania cieczy. Dodatkowo należy uwzględnić koszty konserwacji i serwisowania urządzenia, które są niezbędne dla zapewnienia jego prawidłowego działania.
Jakie są kluczowe aspekty bezpieczeństwa przy pracy z destylatorami przemysłowymi
Bezpieczeństwo pracy z destylatorami przemysłowymi jest niezwykle istotnym zagadnieniem, które powinno być priorytetem dla każdej firmy zajmującej się tego typu procesami. Praca z substancjami chemicznymi wiąże się z ryzykiem wystąpienia niebezpiecznych sytuacji, takich jak pożary czy wybuchy spowodowane parowaniem łatwopalnych cieczy. Dlatego kluczowe jest przestrzeganie odpowiednich procedur bezpieczeństwa oraz stosowanie właściwych zabezpieczeń technicznych. Należy zapewnić odpowiednią wentylację pomieszczeń, w których znajdują się destylatory, aby uniknąć gromadzenia się szkodliwych oparów. Ważne jest także regularne szkolenie pracowników dotyczące zasad BHP oraz postępowania w sytuacjach awaryjnych. Każda firma powinna posiadać plan ewakuacyjny oraz procedury reagowania na awarie lub incydenty związane z użytkowaniem destylatorów. Dodatkowo warto inwestować w nowoczesne technologie monitorujące parametry pracy urządzeń, co pozwala na szybką detekcję nieprawidłowości i minimalizację ryzyka wystąpienia niebezpiecznych sytuacji.
Jakie są przyszłe kierunki rozwoju technologii destylacji przemysłowej
Przyszłość technologii destylacji przemysłowej zapowiada się bardzo interesująco dzięki dynamicznemu rozwojowi innowacyjnych rozwiązań technologicznych oraz rosnącej świadomości ekologicznej społeczeństwa. Jednym z kluczowych kierunków rozwoju będzie dalsza automatyzacja procesów produkcyjnych, co pozwoli na zwiększenie efektywności oraz redukcję kosztów operacyjnych. Wprowadzenie sztucznej inteligencji do monitorowania i optymalizacji procesów destylacyjnych może znacząco poprawić jakość uzyskiwanych produktów oraz skrócić czas reakcji na ewentualne problemy techniczne. Równocześnie rośnie zainteresowanie technologiami przyjaznymi dla środowiska, które pozwalają na zmniejszenie zużycia energii oraz ograniczenie emisji szkodliwych substancji do atmosfery. W tym kontekście rozwijają się technologie odzysku ciepła oraz innowacyjne metody separacji oparte na membranach czy adsorpcji. Ponadto coraz większą rolę odgrywa zrównoważony rozwój i gospodarka o obiegu zamkniętym, co skłania producentów do poszukiwania nowych sposobów wykorzystywania odpadów powstających podczas procesów produkcyjnych.