Maszyny pneumatyczne to urządzenia, które wykorzystują sprężone powietrze do wykonywania różnorodnych zadań. Ich budowa opiera się na kilku kluczowych elementach, które współpracują ze sobą, aby zapewnić efektywność i niezawodność działania. Podstawowym elementem jest kompresor, który spręża powietrze i dostarcza je do systemu. Kompresory mogą być różnego rodzaju, w tym tłokowe, śrubowe czy wirnikowe, a ich wybór zależy od specyfiki zastosowania. Kolejnym istotnym komponentem jest zbiornik na sprężone powietrze, który gromadzi powietrze i utrzymuje jego ciśnienie na odpowiednim poziomie. Zbiorniki te są często wykonane z wytrzymałych materiałów, aby wytrzymać wysokie ciśnienie. W systemie pneumatycznym niezbędne są także zawory, które kontrolują przepływ powietrza oraz siłowniki, które przekształcają energię pneumatyczną w ruch mechaniczny. Siłowniki mogą być cylindryczne lub membranowe i są kluczowe dla działania maszyn.
Jakie są zastosowania maszyn pneumatycznych w przemyśle
Maszyny pneumatyczne znajdują szerokie zastosowanie w różnych gałęziach przemysłu ze względu na swoją wszechstronność i efektywność. W przemyśle produkcyjnym wykorzystuje się je do automatyzacji procesów montażowych oraz pakowania produktów. Dzięki precyzyjnemu działaniu siłowników pneumatycznych możliwe jest szybkie i dokładne wykonywanie operacji, co znacząco zwiększa wydajność produkcji. W branży budowlanej maszyny pneumatyczne są wykorzystywane do prac takich jak wiercenie, cięcie czy kucie betonu. Narzędzia pneumatyczne, takie jak młoty udarowe czy wiertarki, charakteryzują się dużą mocą oraz mobilnością, co czyni je idealnymi do pracy w trudnych warunkach. W logistyce i magazynowaniu maszyny pneumatyczne służą do podnoszenia i transportowania ciężkich ładunków za pomocą systemów podnośników czy chwytaków. Ponadto w sektorze motoryzacyjnym stosuje się je do testowania komponentów oraz w procesach lakierniczych.
Jakie są zalety i wady maszyn pneumatycznych
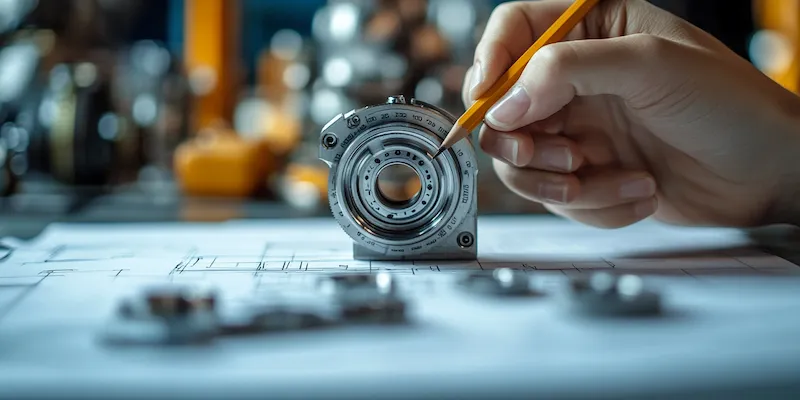
Maszyny pneumatyczne mają wiele zalet, które sprawiają, że są popularnym wyborem w różnych branżach przemysłowych. Jedną z głównych korzyści jest ich prostota konstrukcji oraz łatwość obsługi. Systemy pneumatyczne są zazwyczaj mniej skomplikowane niż hydrauliczne czy elektryczne, co ułatwia ich serwisowanie i naprawy. Ponadto maszyny te charakteryzują się dużą mocą przy stosunkowo niewielkiej wadze, co czyni je mobilnymi i łatwymi do przenoszenia. Kolejną zaletą jest bezpieczeństwo użytkowania; sprężone powietrze nie stwarza ryzyka wycieków substancji toksycznych ani pożarów. Jednakże maszyny pneumatyczne mają również swoje wady. Wymagają one stałego źródła sprężonego powietrza oraz odpowiedniej infrastruktury do jego dostarczania, co może wiązać się z dodatkowymi kosztami. Dodatkowo efektywność energetyczna systemów pneumatycznych bywa niższa niż innych rozwiązań, takich jak hydraulika czy napędy elektryczne.
Jakie są nowoczesne technologie w budowie maszyn pneumatycznych
W ostatnich latach rozwój technologii wpłynął na sposób budowy i funkcjonowania maszyn pneumatycznych. Nowoczesne rozwiązania pozwalają na zwiększenie efektywności oraz precyzji działania tych urządzeń. Jednym z najważniejszych trendów jest automatyzacja procesów związanych z obsługą maszyn pneumatycznych. Dzięki zastosowaniu zaawansowanych systemów sterowania możliwe jest zdalne monitorowanie pracy urządzeń oraz optymalizacja ich działania poprzez analizę danych w czasie rzeczywistym. Wprowadzenie technologii Internetu Rzeczy (IoT) umożliwia integrację maszyn z siecią internetową, co pozwala na bieżące śledzenie ich parametrów oraz przewidywanie ewentualnych awarii przed ich wystąpieniem. Kolejnym innowacyjnym rozwiązaniem jest zastosowanie materiałów kompozytowych oraz lekkich stopów metali w konstrukcji elementów maszyn, co przyczynia się do zmniejszenia ich masy oraz zwiększenia odporności na uszkodzenia mechaniczne. Dodatkowo rozwijane są nowe typy siłowników o większej wydajności energetycznej oraz mniejszych wymiarach, co pozwala na bardziej kompaktowe projektowanie systemów pneumatycznych.
Jakie są najczęstsze problemy w eksploatacji maszyn pneumatycznych
Eksploatacja maszyn pneumatycznych, mimo ich licznych zalet, wiąże się z pewnymi problemami, które mogą wpływać na ich wydajność i niezawodność. Jednym z najczęstszych problemów jest wyciek sprężonego powietrza, który może prowadzić do znacznych strat energetycznych oraz obniżenia efektywności działania systemu. Wyciek taki może występować w miejscach połączeń, uszczelek czy zaworów, dlatego regularne kontrole i konserwacja są kluczowe dla utrzymania sprawności maszyn. Innym istotnym problemem jest zanieczyszczenie sprężonego powietrza, które może prowadzić do uszkodzenia elementów roboczych oraz obniżenia jakości wykonywanych operacji. Z tego powodu stosowanie filtrów oraz osuszaczy powietrza jest niezbędne w każdym systemie pneumatycznym. Kolejnym wyzwaniem są awarie komponentów, takich jak siłowniki czy zawory, które mogą wynikać z niewłaściwego użytkowania lub braku odpowiedniej konserwacji. Warto również zwrócić uwagę na kwestie związane z ciśnieniem roboczym; zbyt niskie ciśnienie może prowadzić do niedostatecznej mocy urządzeń, natomiast zbyt wysokie może powodować uszkodzenia.
Jakie są różnice między maszynami pneumatycznymi a hydraulicznymi
Maszyny pneumatyczne i hydrauliczne to dwa różne typy systemów napędowych, które mają swoje unikalne cechy oraz zastosowania. Podstawową różnicą między nimi jest medium robocze; maszyny pneumatyczne wykorzystują sprężone powietrze, podczas gdy hydrauliczne korzystają z cieczy, zazwyczaj oleju. Ta różnica wpływa na sposób działania obu systemów oraz ich właściwości. Maszyny pneumatyczne charakteryzują się szybszymi reakcjami i mniejszą masą, co czyni je idealnymi do zastosowań wymagających dużej mobilności i szybkości działania. Z drugiej strony maszyny hydrauliczne oferują większą moc i moment obrotowy, co sprawia, że są bardziej odpowiednie do ciężkich prac wymagających dużych sił. Kolejną istotną różnicą jest bezpieczeństwo; sprężone powietrze jest mniej niebezpieczne niż ciecz pod wysokim ciśnieniem, która może stwarzać ryzyko wycieków i pożarów. W kontekście kosztów eksploatacji maszyny pneumatyczne często okazują się tańsze w utrzymaniu, ponieważ wymagają prostszej infrastruktury oraz mniejszych nakładów na energię.
Jakie są przyszłościowe kierunki rozwoju technologii pneumatycznych
Przyszłość technologii pneumatycznych zapowiada się bardzo obiecująco dzięki ciągłemu postępowi w dziedzinie inżynierii oraz automatyzacji. Jednym z kluczowych kierunków rozwoju jest integracja systemów pneumatycznych z nowoczesnymi technologiami cyfrowymi, takimi jak sztuczna inteligencja i uczenie maszynowe. Dzięki tym technologiom możliwe będzie bardziej zaawansowane monitorowanie stanu maszyn oraz przewidywanie ewentualnych awarii na podstawie analizy danych zbieranych w czasie rzeczywistym. Wprowadzenie inteligentnych systemów zarządzania pozwoli na optymalizację procesów produkcyjnych oraz zwiększenie efektywności energetycznej urządzeń. Kolejnym ważnym trendem jest rozwój materiałów kompozytowych o wysokiej wytrzymałości i niskiej wadze, co przyczyni się do dalszego zmniejszenia wymiarów maszyn pneumatycznych oraz zwiększenia ich wydajności. Ponadto rosnące zainteresowanie ekologicznymi rozwiązaniami skłania producentów do poszukiwania alternatywnych źródeł energii dla systemów pneumatycznych, takich jak energia słoneczna czy wiatrowa. Te innowacje mają na celu nie tylko poprawę wydajności maszyn, ale także zmniejszenie ich wpływu na środowisko naturalne.
Jakie są kluczowe aspekty konserwacji maszyn pneumatycznych
Konserwacja maszyn pneumatycznych jest kluczowym elementem zapewniającym ich długotrwałe i bezawaryjne działanie. Regularne przeglądy techniczne pozwalają na wczesne wykrywanie usterek oraz zapobieganie poważniejszym awariom, które mogą prowadzić do przestojów w produkcji. Ważnym aspektem konserwacji jest kontrola szczelności układów pneumatycznych; wszelkie wycieki sprężonego powietrza powinny być natychmiast eliminowane, aby uniknąć strat energetycznych. Niezbędne jest również regularne czyszczenie filtrów powietrza oraz osuszaczy, aby zapewnić odpowiednią jakość sprężonego powietrza dostarczanego do systemu. Dodatkowo warto monitorować stan uszczelek oraz połączeń, które mogą ulegać zużyciu w wyniku długotrwałego użytkowania. W ramach konserwacji należy również przeprowadzać okresowe smarowanie ruchomych części maszyn zgodnie z zaleceniami producenta; odpowiednie smarowanie wpływa na płynność pracy urządzeń oraz minimalizuje ryzyko uszkodzeń mechanicznych.
Jakie są najważniejsze normy dotyczące budowy maszyn pneumatycznych
Budowa maszyn pneumatycznych musi spełniać określone normy i standardy bezpieczeństwa, które mają na celu ochronę użytkowników oraz zapewnienie efektywności działania urządzeń. W Europie kluczowym dokumentem regulującym te kwestie jest dyrektywa maszynowa 2006/42/WE, która określa wymagania dotyczące projektowania i budowy maszyn. Zgodność z tą dyrektywą jest niezbędna dla uzyskania oznaczenia CE, co potwierdza spełnienie norm bezpieczeństwa przez produkt. Ponadto istnieją normy dotyczące jakości sprężonego powietrza, takie jak ISO 8573-1, które definiują dopuszczalne poziomy zanieczyszczeń w sprężonym powietrzu wykorzystywanym w różnych aplikacjach przemysłowych. Normy te obejmują zarówno czystość chemiczną jak i mechaniczną powietrza oraz jego wilgotność. Dodatkowo ważne są normy dotyczące materiałów używanych do budowy elementów maszyn; muszą one charakteryzować się odpowiednią wytrzymałością i odpornością na korozję oraz inne czynniki środowiskowe.
Jakie są perspektywy rynku maszyn pneumatycznych w przyszłości
Rynek maszyn pneumatycznych ma przed sobą wiele perspektyw rozwoju dzięki rosnącemu zapotrzebowaniu na automatyzację procesów przemysłowych oraz innowacyjne technologie produkcji. W miarę jak przedsiębiorstwa dążą do zwiększenia efektywności operacyjnej i redukcji kosztów produkcji, maszyny pneumatyczne stają się coraz bardziej popularnym rozwiązaniem ze względu na swoją prostotę obsługi oraz niskie koszty eksploatacji. Przemiany związane z Przemysłem 4.0 również mają znaczący wpływ na rozwój rynku; integracja systemów pneumatycznych z nowoczesnymi technologiami informacyjnymi umożliwia lepsze zarządzanie procesami produkcyjnymi oraz optymalizację wykorzystania zasobów energetycznych.